Home Mechanic: Electrical Corrosion on Connectors
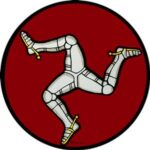
Home Mechanic: Electrical Corrosion on Connectors
The quality of the BMW harnesses, switches and relays is very, very high. Switches like the Neutral switch on the gearbox and the Clutch Release switch built into the clutch lever obviously get millions of actuations and wear out. But common issues like turn signals acting up, or horns you can barely hear can be as simple as loss of electrical connectivity. Before you invest big money in replacing entire sections of electrical harness with great struggle or great expense, there is a very good chance that the cure for the electrical fault lies somewhere else in the circuit.
I have found that simple connector terminal corrosion has a much higher probability of being your issue. What I would suggest is that BEFORE you spend big bucks on new electrical components, or on headache remedies (because you took the alternator or handlebar switches apart) is that you read and try this this simple solution first.
Explanation
The root issue is that automotive grade connectors use a thin zinc plating over brass. Bare brass will easily develop a green oxide over time (witness the Statue of Liberty), which will impede electrical connectivity. And so a flash coating of zinc is usually added to the brass before or after the forming of the contact. Zinc is the industry favorite because it does not pollute, is cheap, and has no adverse health issues. Zinc makes the electrical connectivity last longer, but over time even zinc begins to have issues. (For more information on aging of electro-deposited zinc research: dendritic growth in zinc connectors)
In the classic Airhead (usually in the range of 40-50 years old) we have the 4 decades of riding in the rain and wash water getting into the electrical connectors plus the natural breakdown of the zinc due to simple aging. The results that I have experienced in my personal and professional Airhead repair is that parts of the electrical system become intermittent and/or stop working completely.
Suggested Action
Buy the smallest container of electrical connector anti-oxidation compound, such as No-Ox-Id by Sanchem, that you can find. Even the 1oz tub of this stuff is under $7 on Amazon. Skip the dielectric paste and buy a real de-oxidizer like a professional electrician would use. The difference is that the de-oxidizer 1) promotes electrical connectivity AND 2) provides a preventative barrier against future corrosion. Because of the anti-oxidation action the amount of compound needed on each contact is minimal. The 10cc tube shown below is enough to completely service 3 Airheads.
Professional Anti-Oxidation Compound
[ I suggest that you do not select a "dielectric paste". A "dielectric" by its very definition is an electrical insulator, that which stops electrical connectivity. Our goal is to improve electrical connectivity. A dielectric compound might be helpful on a new electrical system where we might want to exclude water to prevent problems. But the time for prevention on a 40 year old Airhead is well past. ]
Corrective Steps
Open up your main connector area. On most Airheads this will be the inside the headlamp. With the aid of a bright lamp (so that terminals and wire colors can be easily identified) and a skinny pair of pliers (such as "duck bill" pliers)... disconnect every wire one at a time from the multi-color circuit board in the back of the headlamp shell in an orderly fashion. Apply a very small amount of anti-oxidation compound (the volume of one liquid drop) inside the female terminal, and then re-plug the wire to the same prong from which it was removed. The wire color and the circuit board color should match, if you get stymied.
Main circuit board found on most Airheads
This may cost you 20 minutes and a few dollars, but the changes are usually miraculous. Horns get louder, lights get brighter... in summation, all sorts of good things start to happen. And in truth, until you take this basic step, all other changes may be useless.
Then make the same application on the 2 fuse ends, all relay terminals, all 4 battery connections, the 3 voltage regulator terminals, the connection between the 2 harness sections next to the battery... in short... ANY electrical connection you happen to work on can be improved by adding a small amount of this compound during re-assembly. If you will consistently do this during routine maintenance, within a short time the entire bike will end up treated and restored to 100% perfect electrical flow.
And it sure beats purchasing expensive German electrical components that you cannot return.
Hope this helps.
Owning an old Airhead is easy.
Keeping an old Airhead running great is the true test.
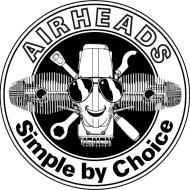
Good advice, thanks.
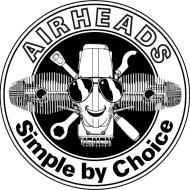
Thank you for your advice! I did just that!

I need to buy some of that goop to give this a go.
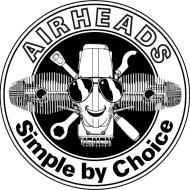
Got around to doing this task yesterday. Things looked like new inside the headlight, of course its well protected inside the RS fairing headlight tunnel. Skipped a few of the headlight board plugs that were hard to get at but lightly Sanchem-greased most of them along with what I assume are the headlight and blinker relays ('84). Four or five under-tank connectors, another by the battery/subframe, starter relay, voltage regulator. Left the ignition module alone after failing to figure out how to get it unplugged. The little tabs on the sides wouldn't respond to pressure. Also didn't touch the coils although I'll probably go back and do them since the tank won't be going back on until Spring.
Is there any reason NOT to do the high voltage parts eg coils & ignition module? (Battery is disconnected)
Removed and disassembled the headlight, removed halogen bulb and the two-pronged "block" in front of it in anticipation of receiving the LED bulb. Surprised by 8 separate bent springs being used to hold pressure between the ring and lens. Seems kinda lame but its held it together for 40 years.
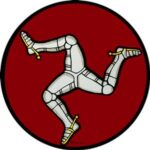
Posted by: @don-walterGot around to doing this task yesterday. Skipped a few of the headlight board plugs that were hard to get at but lightly Sanchem-greased most of them along with what I assume are the headlight and blinker relays ('84). Four or five under-tank connectors, another by the battery/subframe, starter relay, voltage regulator. Left the ignition module alone after failing to figure out how to get it unplugged. The little tabs on the sides wouldn't respond to pressure. Also didn't touch the coils although I'll probably go back and do them since the tank won't be going back on until Spring.
► The ignition module has a VERY thin, black steel spring wire that has to be removed before the connector can be unplugged. This "steel wire" acts like a one-way clip, allowing you to plug the harness into the module, but keeping it from unplugging itself. However, this is a computer-grade connector and seems to have gold-plated contacts... so it needs little if any No-Ox. BUT... you need to disconnect that connector so that you can dismount the module from the frame and renew the Heat Sink paste (aka "thermal paste") between the module and frame. If the transistors inside the ignition module cannot shed their heat, then the module will self-destruct. I believe the heat sink paste of choice for the guys that build the super-fast gaming computers goes by the name of "Artic Silver". Click Here.
To apply new thermal paste, first you need to sand off the OEM paste (which has now hardened into a brown varnish) from both surfaces. When both surfaces are bright, shinny, and spotlessly clean, apply about 2 drops of compound and use a stiff plastic tool (like a credit card) to apply a smooth, VERY even coating across 100% of the transfer surface. Then, carefully apply EQUAL torque to the mounting bolts.
► While under the tank, don't forget to No-Ox the main "Ground" bonding point, which is the 3 or 4 Brown wires attached with a ring lug on the 2 bolts that mount the LH ignition coil. You'll want to coat that entire bolt, threads and all. It's VERY important that the ring lug bond 100% to the bolt, which needs to bond 100% to the frame in order to Return all electrical power back to the alternator and battery.
(Some super-resourceful types will add a 12" Brown wire [with 1/4" ring lugs on both ends] between the second ignition coil bolt going back to the battery Negative terminal. This step takes the frame out of the circuit almost completely.)
Posted by: @don-walterIs there any reason NOT to do the high voltage parts eg coils & ignition module? (Battery is disconnected)
► The high voltage of the ignition coil secondary will typically have zero issues getting the 25,000V to overcome any corrosion. However, since the individual ignition coils face forward, there will always be the chance that water can enter the boot around the plug wire and short the high voltage to ground. So, adding No-Ox to all the coil terminals (both low and high voltage) will be an excellent deterrent to water intrusion.
Posted by: @don-walterRemoved and disassembled the headlight... Surprised by 8 separate bent springs being used to hold pressure between the ring and lens. Seems kinda lame but it's held it together for 40 years.
► That's the way headlamp reflectors have been held in most brands of motorcycles since at least the 1930's. Simple and efficient. I've seen as few as 3 clips used per reflector.
Hope this helps.
Owning an old Airhead is easy.
Keeping an old Airhead running great is the true test.
- 27 Forums
- 1,922 Topics
- 10.9 K Posts
- 2 Online
- 6,016 Members