85' 80RT exhaust flange damage
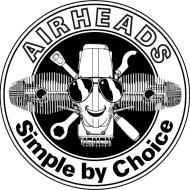
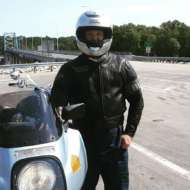
There are machine shops that will saw the old flange off and weld on a new one. I'm not sure about the cost.Â
This is a tool I use in my actual job that I've had very good results with. Never tried it in that application.
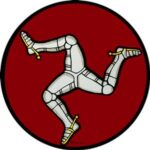
Never ever assemble the exhaust flange onto the cyl head without a fresh coating of high temperature "never-seize". The alloy in the head and the alloy of the flange are just similar enough that they have a very high affinity for each other. "Seizing" and "galling" are simply terms that describe the transfer of metal from one part to the other, much akin to welding... and just as permanent.
The only way to separate the 2 parts now is to slowly cut away the finned exhaust nut with a Dremel tool. The sections that have not become part of the cyl head will fall right off.
You can buy a die to clean the threads after-the fact, but the one-time way is called a "thread file". Either way you need to exactly match the tool to the threads (in this case metric) to get good results.Â
The numerous "never-seize" products work by breaking the "similar metal" kinship bond by laying down a dis-similar metal in the threaded joint. Threads by their nature are very close-fitting, and so the compound MUST be re-applied each time the part is being re-installed. This warning is part of every BMW manual and every Chris Harris Airhead repair video.Â
I believe this is the product Chris Harris uses.  I prefer the nuclear grade product with nickle  .Â
The product is also useful on spark plug threads and several other places on an Airhead. These include exposed fasteners that might need to be loosened on the side of the road for emergency repair.
Hope this helps.
Â
https://www.youtube.com/watch?v=ZRXKC9Yxfug
Owning an old Airhead is easy.
Keeping an old Airhead running great is the true test.
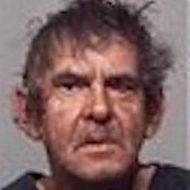
I recall the warnings about exhaust flange thread seizing from days of old. I recently bought my first Airhead since about 15 years ago, a 1995 with 25,000 miles. One of the first things I did was gently break the nuts loose and screw them off, and slather antiseize on both the nuts and head flanges. My practice is, about once per year, back the nuts off about 1/2 turn, then retighten. That, along with the generous coat of anti seize, will hopefully keep them from ever seizing. Â Â Â
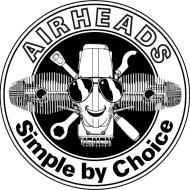
There should be a die available somewhere to match this thread pitch. I do not own one myself. You might try contacting one of our advertisers to check in to a repair, or to find out what the thread pitch is. If I ever had that problem with a bike I owned, I would just pony up the dough to get the correct tool. That way, I would always have it, and might loan it to other members. There was some talk recently about compiling a tool loan list. Â
former Airmarshal, IL.
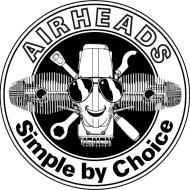
O.K., I went outside and cleaned out the gutters on my house and thought this over for a bit. I decided to bump around other Airhead web sites and found the following thread on Adventure rider. it is from 2013.
https://advrider.com/f/threads/stripped-exhaust-threads.875498/
Among other info in the thread, the thread pitch is described as 52x2, in mm of course. If you decide to purchase or borrow a die for the purpose of chasing the threads, I'd put the odds at 50/50 for a successful result depending on how bad the original threads are damaged.
Â
former Airmarshal, IL.
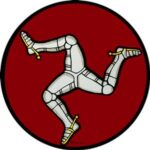
The correct thread designation is: M55x2
Mcmaster-Carr and other tooling sources max out around 35mm. However, there is a seller on Ebay with one for $70.
https://www.ebay.com/itm/114303414587
Owning an old Airhead is easy.
Keeping an old Airhead running great is the true test.
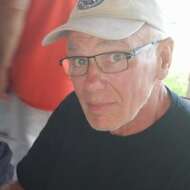
I bought a die on Ebay out of Belarus, $40. Russian made, luckily only cutting aluminum. Welded it onto an old Snap-on socket and saved the threads on my daughter's R80. As long as the threads aren't boogered too bad the die will do fine.
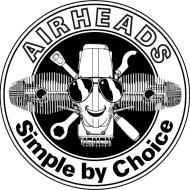
I thot I had replied to this old thread with my solution. I guess not. Anyway, just in case anyone else is dumb enough (like me!) to beat off one of these exhaust nuts.
SO.... First. If it gives you even THE SLIGHTEST fight in coming off. Stop. Get a die grinder/cutter and cut the nut off. (see various youtube videos). You are going to be buying a new nut anyway, why thrash the head.
Next thing I did. bought a "Thread file". Metric. It has every possible thread pitch you may need.
Next thing I did. bought a rotary "Stone" for my die grinder that had the "Vee angle" of the thread.
Dug out my biggest bestest magnifiying glass and shop lighting. Got my chair right there so I was like a dentist doing a root canal.
I just carefully and slowly started dressing the threads on the head as best i could with the file. No hurry and from every attack angle I could get at it. Had it all looking pretty good, so it was time to try to thread on the NEW nut. Slowly and straight on.... NOPE! The head didn't really have a good "Lead-in" thread. The first one the nut needs to grabl Lots of back and forth, comparing the still good right cylinder head with the buggered up Left one I was working on. Got the new thread angle rotary stone. Carefully tracked the threads round and round and round until I figured where it just faded away. This is where I needed to dress it a bit and make a more defined thread for the nut to grab on it's initial "Bite". Success!!! Hand tighten only at this point. Took it off and slathered up with the copper anti-seize. Snugged it up. hope it's easier next time it comes off!!!
Brad
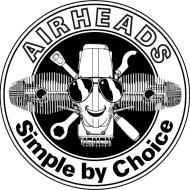
Forcing it is bad news, but if not too severely damaged, you can use a thread repair file.Â
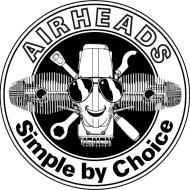
Sorry, posted this without having read your last post. I too learned the value of copper slip paste and metric thread files the hard way! R
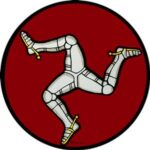
If you ever feel any resistance, you'll want to STOP! immediately and cut the flange off. The reason is that typically the damage is HIGHLY localized. A small spot, usually no larger than 1/4 inch, is causing all the trouble. By cutting the flange off, you end up saving all the "good threads" and minimizing your repair efforts to that tiny area.
If you insist on forcing the flange, the ruined area will simply be dragged across a much larger area and end up destroying "good thread". The $20 flange is toast at the first seizure. Forcing it off is simply killing the much more expensive cyl head and converting a short "home repair" into a professional "send it away and wait" type repair.
Owning an old Airhead is easy.
Keeping an old Airhead running great is the true test.
- 27 Forums
- 1,922 Topics
- 10.9 K Posts
- 3 Online
- 6,016 Members