75/5 F.D. How to remove staked pinion bearing?
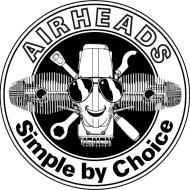
1st post here. I have a 72' 75/5 trying to remove the FD pinion needle bearing. Mine has a solid pin that stakes the outer bearing race into the bearing pocket. The pin has a very tiny recess cut into it to pull from. of which only a small area is even exposed to grab. With a Lupe there is a visible slight crack in the upper / thinner part of the casting. do I need to be concerned with this? Before I do something stupid I figured Id ask for a possible procedure. Only thing I have found on the internet is people who have destroyed it and ultimately abandon bearing replacement. Lastly reason for the change out is after inspection I found the outer roller cage has a tiny split in it.
Thanks in advance! Ian S
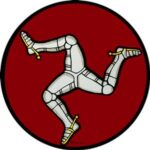
First understand, I have never done this repair. The following is my best guess after reviewing exploded diagrams of the final drive housing.
• Since this pin resides in a blind hole, most removal methods are going to be based on drilling or milling the pin out. First step then is to order 4 replacement pins and experiment to determine just how hard is "hard". I give a vey low probability of success with this method.
• Drilling the pin will require more than your normal HSS home drill bit selection. The pin is proabably fairly hard and a small diameter (about 3mm).
► The only other solution is to drill a new hole in the outside housing which accurately aligns with the pin and tap out the pin from the outside (going toward the inside) with a drift. This option is a near impossibility without a milling machine, a holding stand that keeps the housing stable and the ability to make VERY accurate measurements.
I might drill a 3/16" (0.187") hole, knowing that even a near miss will still expose enough of the (0.118") pin to offer access with a small drift (while the housing is at an elevated temperature). Then this hole can be re-sealed using any number of filler epoxies (like JB Weld) and 3/16" will be easy to hide and almost invisible.
• The removal process may be assisted at some point during the process by heating the FD housing. With castings this size, I greatly prefer hot plates, convection ovens, and/or boiling water to old-school processes like torches. You'll get much better results with the part being more evenly heated.
►► This exercise is going to be filled with pitfalls and all sorts of hidden traps. Let's say you do manage to get the pin out and your bearing replaced... what then ? Pinion bearing replacement is going to necessitate pinion shimming which takes another complete set of exotic measuring tools, including an assortment of shims, 10 thousandths reading dial indictors on magnetic bases, etc. Ring and pinion replacement and setup is specialist work. I have 40 years of motorcycle repair experience, a degree in mechanical engineering, a full set of dial indicators, and access to a Bridgeport vertical mill, etc.... and I would never attempt this job. If this was my bike, I'd be buying another final drive off eBay and getting on with life. There are too many used FD housings laying around and a very low demand. Surely several can be found for a very reasonable price.
Owning an old Airhead is easy.
Keeping an old Airhead running great is the true test.
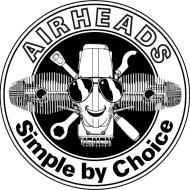
Thanks Richard. I appreciate the reply. The impetus for removing this bearing is that is has a cracked cage. Who knows, maybe its run like this for years? maybe it can still be run? the needles are in great shape. if a 32K mi. example w known history so im confident on the milage. The idea was to simply strip the FD to be sent out. The reason this ever came apart in the 1st place was it went out to Hansens for spline rebuild and new drive dog riveted into rear wheel. original plan was to pre measure, set new large bearing, take new measure and shim (or hopefully not) and run it. Of course well intentioned well ok replace seals etc etc and now im deep into it. Apparently this arrangement of stake pin was short lived from what I can tell? they later went to a set screw.
To be clear is your suggestion to find a new FD that Does NOT have that pin? Or try and just run a replacement? At min I would have to get the drive set up to make use of the new large bearing and spline work. Otherwise all was for not.
I am attaching a picture of the cracked shell and maybe I run it based on responses. crack is a 12 o clock
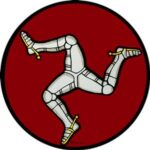
Thanks for the very clear photo.
• The "crack" is in the needle bearing CAGE, not the race. The cage keeps the bearings from touching each other as they roll. If the cage wasn't there to separate, then the clockwise rolling surface of one needle would roll up against the counter-clockwise rolling surface of the adjacent needle.... which would cause problems. So the cage must be there to protect the individual rollers from each other.
• There is only one reasonable way to make the cage, which is "in the flat". After all the holes are added for the needle rollers, then the part is rolled into a C-shaped cylinder. There is no need to bond the 2 ends of the cage together because there is no reason to. There are zero forces present which will harm the cage. In fact, because the rollers themselves are being spaced apart by the cage, leaving a small gap between the 2 ends of the cage is an advantage in that the rollers are free to "find their own center".
• So what you are seeing is most proabably the meeting place of the 2 manufactured ends of the C-shaped cage, and not a "crack" or other mishap. And this explains why you don't see any associated pitting or galling, which one would certainly expect if the bearing race really had experienced a destructive crack.
Bottom Line: Great inspection technique on your part, but in this case a false alarm. There is no need for any action other than reassembly with new seals and synthetic gear oil.
Owning an old Airhead is easy.
Keeping an old Airhead running great is the true test.
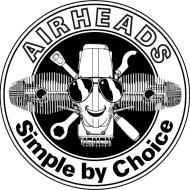
Thanks again. OK, All makes sense. Having thoroughly inspected the other end of the cage I see no such split. Hence the concern. I generally came to the same conclusion you did, thinking, well, this isn't really a serious issue. However I am a do it once, do it right guy. So my instinct is to replace anything suspect I can while I'm in there and thinking how hard can it be to remove a stupid bearing! Thanks for putting me much more at ease. I do ride this bike some distances so reliability is paramount. I guess if I were to have a concern if any, would be that since (from what I can tell) this is in fact a one piece cage (probably welded) one more break / crack means it comes free and then I would be on eBay, but as you said they are abundant.
Thanks ! Ian
- 27 Forums
- 1,922 Topics
- 10.9 K Posts
- 2 Online
- 6,016 Members