S Fairing Repair
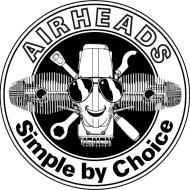
I have an S fairing from BMW. This is not an aftermarket fairing. It is cracked where the dash joins the fairing body. The prior owner attempted a repair using glue or epoxy. I ground out the glue to effect repair using fiberglass and it appears that the dash section may be plastic. Now I am questioning the materials used in the body of the fairing as well. Can anyone give me information regarding the materials used in these fairings? If anyone has ideas for my project please offer suggestions.
Thank you in advance,
Tom
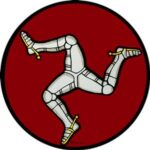
While we may refer to these fairings as being "fiberglass", they are more correctly an automotive plastic with a glass filler. I have had very good luck in the past making repairs with filler epoxies like JB Weld. I like these because there is no hurry, and should the break go all the way through it can be sanded and painted like an exterior body filler.
Owning an old Airhead is easy.
Keeping an old Airhead running great is the true test.
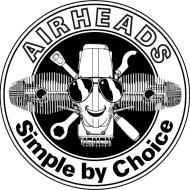
Thank you for your response Wobbly. I have never used JB Weld. If I remember correctly it comes in a tube like tooth paste. When I was cleaning and sanding it seemed like the dash and the fairing body are 2 different materials. I have learned that they are separate pieces and put together with rivets or grommets. I am toying with the idea of separating the dash from the fairing and replacing the dash but not having a complete understanding of how the pieces are joined causes hesitation. I will look further into Haynes and Chilton to see what I can learn. I guess I should have started there. I will post what I find. More info from the forum is always welcome as information is in the books but wisdom is on the forum. Thanks again for your help.
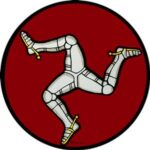
► Apologies, I possibly misunderstood which item was damaged. I would not try to repair the dash, but instead replace it. There are always good used units on Ebay. It was the fairing body I had successfully repaired using filler epoxies, such as JB Weld.
► Actually, I believe you DO want to separate the dash from the fairing. As stock they are riveted together with a hollow metal rivet that allows the windscreen to be attached. In my humble opinion there are much better components available for this job that were not around when this fairing was introduced.
Today you'll want to use a product called a "Well Nut" (available on Amazon). [McMaster-Carr lists them as "Rubber-Insulated Brass Rivet Nut". See product 93495A250.] Either in M5 or 10-32 UNF (they are nearly identical either way).
These amazing items install from the outside and have the capability to pull the dash up to the fairing, much like a "pop rivet" pulls 2 pieces together upon tightening. Then you lay your windscreen atop the rubber washer left by the Well Nut, and attach the windscreen with (black) nylon screws in M5 or 10-32 to match the thread inside the Well Nut. The screw ends up pulling all 3 parts together, all with no nut to hold on the inside. Additionally, the windscreen ends up being supported about 2mm off the fairing, which keeps dust, pollen, dirt and water from trapped on the dash.
Section View of how a Well Nut works
The absolute BEST thing about these Well Nuts is that it allows windscreens to be changed in minutes. This is nice on an S fairing, but it's an absolute God-send on an RS where the inside nuts are almost impossible to reach. So with that added ease, you could have high and low windscreens that change with the weather, or different colors. Why not if you have the capability to change one out using only a screw driver in about 2 minutes ?
Hope this helps.
Owning an old Airhead is easy.
Keeping an old Airhead running great is the true test.
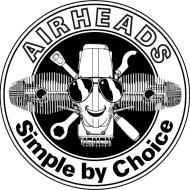
Thanks Wobbly! This is great information. Now I understand how it is put together so I can take it apart knowing I am not taring it up. That is, of course, unless I tare it up anyway. Nothing ventured, nothing gained. I will look up "Well Nut" on Amazon. The product numbers help me so much I don't know what to say other than thank you thank you!
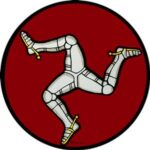
Yeah, It's really no fun disassembling a Humpty Dumpty. So having the Well Nut info lets you drill out BMW's hollow rivets because you have a way to put things back together.
BTW, the reason the Well Nut doesn't spin is that the rubber is inserted into a snug-fitting hole. For the #10 SAE and M5 metric size (what your windshield is looking for), the correct hole size in the fairing and dash board is 3/8". So don't use anything larger than 3/8" drill bit to remove the stock rivets.
If you just want to see and feel a Well Nut, Lowes and Home Depot have them in the hardware drawer section, but they are very expensive by the small bag, AND they typically only carry #10-24 which you can't get a nylon screw for. Remember, to keep the plastic parts from cracking, only rubber and nylon can touch the fairing, dash board, and windscreen. With the vibration of a motorcycle, anywhere steel touches plastic, then you'll soon have a cracked and busted part.
Owning an old Airhead is easy.
Keeping an old Airhead running great is the true test.
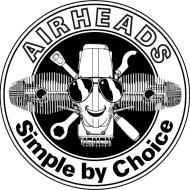
Wow! you are indeed a gold mine of info! Your description of metals touching plastics accounts for other damages I see to this fairing. The location where the mounting arm bolts to the fairing is damaged and it looks as if the previous owner attempted to build up the area with epoxy. It was pretty rough there as if he was trying to control the goop as it set up but it kept running out. He may have attempted multiple layers but it turned into a lumpy mess. I am not sure how I will approach this problem. I could put a thick rubber bushing there or I could try building a form from cardboard and pouring into the mold to match the contours of the mount landing. A rubber bushing may be the most logical. I could take a file to a bushing to match the contours. I am guessing that if there are lateral sustained pressures the fairing could crack so the fairing needs to mount up and fit with out having sustained forces.
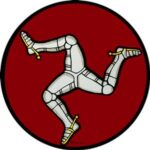
Two things....
• Lots of times those mounting areas break off from the fairing body in an accident. The threaded brass insert may even break loose. That's why I suggest a highly viscous epoxy (typically called a filler epoxy here in my locale), such as JB Weld. You can work it like modeling clay for about an hour after mixing to get it just like you want. Then it will set and can be shaped with Dremel burrs and sanding drums. Hit the inside of the fairing with flat black enamel when everything is ready and the repair completely disappears !!
• One of my secrets (and you can't tell anyone else) is to use flat plumbing faucet repair washers on 5mm and 6mm junctions such as yours. These come with a hole just right for 5mm, and a paper punch can easily open them up for 6mm. You can buy these black neoprene faucet repair washers in a 15 pack at any hardware store for under $2 so it's not only a great solution, it's very cheap to implement.
One of those between the fairing plastic and the mounting L-bracket will stop a lot of issues.
Hope this helps.
Owning an old Airhead is easy.
Keeping an old Airhead running great is the true test.
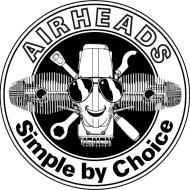
Thanks again Wobbly. I have the front off the bike now and I am stalled for parts and money. I will take this time to get started on the fairing and some wiring harness repairs. This work is doable as you have given me some solutions that are inexpensive. I love it. Thanks so much. This keeps the project moving forward when it would otherwise be stalled.
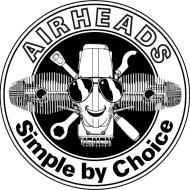
I have used West System Epoxy. They have a variety of fillers and micro balloons to make the epoxy any consistency. They also sell slow and fast hardness.
Good luck
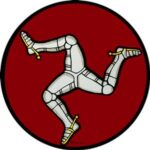
Thanks again Wobbly. I have the front off the bike now and I am stalled for parts and money.
This action violates the first universal rule of motorcycling....
"Ride bike in spring, summer and autumn to pick up chicks and have fun. Work on bike in winter."
Fix it fast or the Classic BMW Police may be knocking on your door. 😛
Owning an old Airhead is easy.
Keeping an old Airhead running great is the true test.
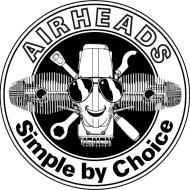
You make a good point here! I am spending weekends in the garage getting ready. JB weld was the way to go for sure as the faring material seems like a hard plastic. The density of JB Weld allowed sanding to come out smooth. The repair work seems to just dissapear leaving a flat smooth serfice ready to paint. You have to work fast though and sometimes the tubes don't get the mix quite right. I had some work cure soft so I removed the material and patched a second time. By taking my time I think the thing will look good as new. It may be a wile for paint still. I will post pictures when I can.
Thanks for the help!
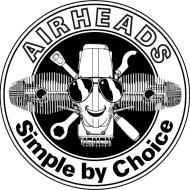
This is an old thread so who knows if anybody will still be interested. But I have a question about the McMaster-Carr rivnuts you describe. They carry two types. The rubber coated insulating rivnut you describe, aka a well nut, seen here: https://www.mcmaster.com/products/inserts/nut-type~rivet/system-of-measurement~metric/insulating-rivet-nuts/
And a screw-to-install rivet nut. These are not insulated, but it’s easy to throw a plastic washer on there and Bob’s your uncle. Here’s the current link to the product page: https://www.mcmaster.com/products/inserts/nut-type~rivet/screw-to-install-rivet-nuts-6/
The real bugaboo with all this stuff, BMW copper rivets or McMaster-Carr rivnuts, is the semi-permanence of them. To take the dash apart from the upper fairing sections, you have to drill them out. I’m enough of a fiddler that I’ll want to take everything apart pretty regularly to, um, fiddle with it.
Is it easy to drill out the McMaster-Carr rivnuts? Or is there another approach to getting them out? The screw-to-install rivnut may be easier to uninstall…maybe by cutting the expanded flange fingers with snips?
Any wisdom on this topic? BTW, I’m working on my 1978 R100RS Motorsport.
—Bill
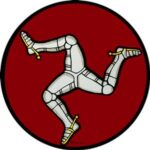
Posted by: @18631Is it easy to drill out the McMaster-Carr rivnuts? Or is there another approach to getting them out? The screw-to-install rivnut may be easier to uninstall…maybe by cutting the expanded flange fingers with snips?
Any wisdom on this topic? BTW, I’m working on my 1978 R100RS Motorsport.
Bill -
Do not get the Wellnut mixed up with the Rivnut !!
► The Wellnut "body" is an neoprene style elastomer; it's NOT a metallic rivet. Therefore, anytime the screw is removed the bulb in the Wellnut completely relaxes and the 2 parts can be separated without issue. If you plan to do this job regularly, then coating each Wellnut with a dab of silicone grease will make assembly/disassembly much easier.
https://www.youtube.com/watch?v=QIOf-7WAZ5E
► The Rivnut operates like the Wellnut, but it is a totally, 100% metallic body. It therefore takes a special puller to exert several tons of pressure to "upset". And once installed and upset, there is no way you will be casually disassembling the Rivnut. As a machine designer and ME, I used the Rivnut on military vehicles. That's the strength range and application these fasteners were designed to fit. I've never owned a Motorsport, but I don't think it's in the same league with bulldozers and heavy trucks. 🤣
https://www.youtube.com/watch?v=h5i1q7dx9LM
► Instead of enlarging the hole in the fiberglass fairing and plastic dash with a standard 2-flute twist drill, I highly recommend using a fine tooth bullet-nose grinding burr. The large cutters of a 2-flute drill bit tend to catch on the soft edges of the fairing and dash hole and either throw the drill bit out (scratching the paint), or catch and crack the plastic. Many small cutting edges make the job go slower, but create a much smoother finished hole in a far more controlled manner.
Lots more videos on both fasteners. I simply picked the first one I came to.
Hope this helps.
Owning an old Airhead is easy.
Keeping an old Airhead running great is the true test.
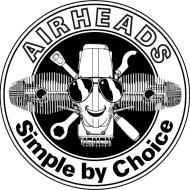
Yes, this really does help. I did not know that a wellnut had a rubber shank. I figured it was rubber coated metal.
I love this solution. Appreciate the tip on (not) drilling, too.
One last question: what length do you use to effectively capture the dash and fairing? I’m thinking the 4 - 10mm, p/n 93495A616.
—Bill
- 27 Forums
- 1,900 Topics
- 10.8 K Posts
- 4 Online
- 5,936 Members