'77 R100: Stripped Camshaft End
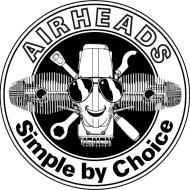
I need some helpful advice on my stripped camshaft threads. A couple of years ago I purchased an early production 1977 R100/7 and decided to tackle some items this winter that could hopefully improve the overall reliability of the bike. As part of these measures, I replaced the clutch pack, the engine and trans were partially resealed, new swingarm bearings installed and I rebuilt the carbs. After reinstalling the carbs the bike fire right up.
Next step was to do the final carb tuning. I talked to a fellow Airhead friend, as well as watching some videos and reading, and learned I should set the points and timing before tuning the carbs. In hopes of doing everything right I decided to add some grease to the backside of the points as well as the lobed shaft on the centrifugal timing advance. The problem showed up when I put to advance back on and tried to reinstall the wave washer followed by the nut. Everything seemed fine until the nut bottomed out and wouldn't tighten up. I knew this only needed to be slightly tightened and made sure not to get go overboard. But, it didn't seem to matter.
I have to assume the threads may already have been stripped or were really close. Or at least that's what I'm telling myself. Honestly, I felt sick afterwards. I've already sunk some decent time and money into this thing this winter and was hoping to be near the end, for now. Overall, everything I've done to bike has gone pretty well. It's apparent the previous owner's maintenance could have been better, but this seems to be the first major issue I've run into.
I tried doing searches on the subject, but haven't come up with anything. Snowbum's article on camshafts only discusses what to do when the tip actually breaks off, rather than becoming stripped. There have to be others that have had this problem. After I found out it was stripped, I just walked away to give myself some time and space to figure out my next move. In my mind, the best case scenario is the engineers at BMW realized how crucial these camshaft threads are and decided to make the nuts softer and the weaker of the two. Obviously I could replace the camshaft. But not only is that likely above my current skill level, it pretty much outside the current limits of my wallet as well.
In trying to figure out what other options I have, it does seem I could convert to an electronic ignition system that attaches to the crankshaft, rather than the camshaft. But again, quite a few more dollars. Or I could just leave it alone and see if it stays put. Not sure I could handle worrying about that one. If anyone else has dealt with this before, please let me know how you resolved it.
Appreciate the help,
J.T.
[Mods altered tile for clarity]
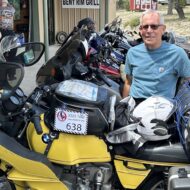
Been thinking about your situation. Had a thought. If the nut will snug somewhat, this might work.
First, I might start with a new nut to get the most bite possible. I would drill and tap the nut to install a small set screw. Snug the nut and tighten the set screw to hold it, with a drop of blue Loctite.
I did something similar to “save” my nearly stripped speedo cable retaining bolt, picture attached. I moved the battery ground elsewhere, so this bolt only needs to be snugged - then retained with the set screw.
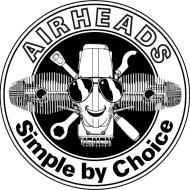
@4949
David,
I like this thought process. It certainly couldn't hurt anything. And, if it eventually stops working, I could always switch to an electronic, crank-based ignition system at that point. Once my wallet has had some time to recover.
As always, thanks so much for your input.
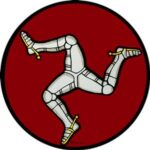
I'm sorry, I'm having a hard time following you. Could you please post some photos ?
Owning an old Airhead is easy.
Keeping an old Airhead running great is the true test.
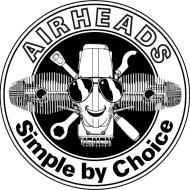
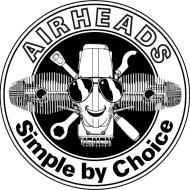
I've attached 2 pics of the area in question. Not sure if I have enough room to drill and tap the nut for a set screw since it's only a M6.
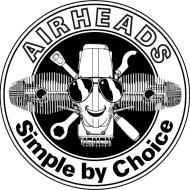
Could you get your hands on an appropriate thread cutting die and chase the threads on the cam tip?, and/or stack a few extra wave washers to change the depth where the nut lands on the tip? The nut doesn't need to be much more than finger tight. Maybe a combination of all the above and a drop of blue loctite?
former Airmarshal, IL.
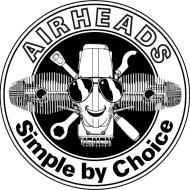
@8053
I did use a die and did the best job possible chasing the treads. It seems to tighten up "hand tight" ok. Maybe I will consider adding a washer or 2 and the loctite. Thanks for the input.
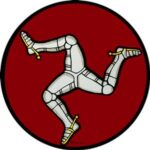
Now I understand ! The tip that fits through the auto advance unit needs repair. Be it broken or stripped, the repair would be very similar, but you have more options than the broken-off edition.
- There's no thrust load on that nut, so you could try using a thread locker or adhesive applied to a new 6mm nut with fresh internal threads. You'd want to de-grease the camshaft end with alcohol or carb cleaner.
- You could file a small groove and fit a wave washer (to hold the AAU in place with tension) and apply a circlip into the groove.
- You could use a die to re-thread the shaft to 5.5mm, 5.0mm or a US thread, something like a #12.
- At one time LocTite made a product for stripped threads... or there's JB Weld.
- Give the AAU your best service, and JB Weld the holding nut into place. With the mileage you're actually going to put on the bike, it's not likely to come up again in your lifetime.
- You could slot a new 6mm hex nut with a metal saw, squeeze it closed, and then braze it in that position, effectively making a ~5.8mm thread.
Remember this nut only holds the AAU in place, so the proper torque is something on the order of 2 ft-lbs (24 in-lbs)... not even "screwdriver tight" !! As long as the AAU stays engaged with the pin that makes it rotate, you're OK.
Some of these suggestions may sound like a 'kludge'. I'm not endorsing any specific idea, I'm just brain-storming ideas in hopes one of them helps you find a solution or conceive of another.
Hope this helps.
Owning an old Airhead is easy.
Keeping an old Airhead running great is the true test.
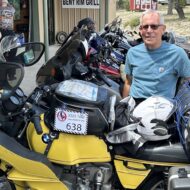
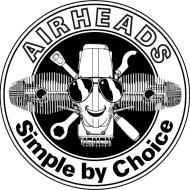
Well, I finally decided to go for broke and give it a whirl. Started by chasing out the old threads with a M6 die. Added a new nut and an additional wave washer, as well as a drop of blue Loctite. I put it on hand tight, plus maybe an 1/8 of a turn. Managed to get the timing set and the carbs somewhat balanced. This was also my first ever carb rebuild.
I was lucky to have a 60 degree day and enough time to put a couple of hours on the bike. Everything seems to be working just fine for now. I decided to try the simplest and easiest "fixes" first and if that doesn't work, then I'll be upping my game. I think re-threading it to a smaller diameter sounds like the best and most "permanent" fix. David, I assume that is what your reference to 4-40 tap was for?
Am looking forward to some consistently better weather to get a better feel for how it's going to hold up.
Thanks for all the helpful advice !
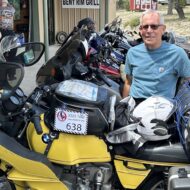
@j-t-sutton No, I was thinking a 4-40 tap might be small enough to install a set screw in an M6 nut. Uses a #43 (.089) drill. I’m not home to check it out myself.
- 27 Forums
- 1,924 Topics
- 10.9 K Posts
- 4 Online
- 6,018 Members