Speedometer cable retaining/battery ground bolt on the gearbox nearing being stripped
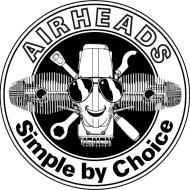
Hello again. Here's another issue with my recently acquired 1978 R80/7.
The [breather] bolt for the gearbox which retains the speedo cable is nearly stripped. I've cut a slot in the battery ground cable as to not have to entirely remove the bolt to disconnect the ground cable, but as I continue to address a few somewhat minor electrical issues (after first disconnecting the ground!), I'm guessing it's eventually going to give up what's left of it's ability to hold even snugly.
I've become aware of various ways of doing thread repairs but does anyone have experience with this particular mounting point (short of removing the engine to have ideal access/angle to install a helicoil)?
Any help will be gratefully appreciated.
Â
Cheers.
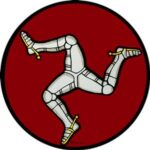
IMHO, the issue stems from the fact that as a battery connection bolt, that bolt must be tight in order to convey the current required for an electric starter motor to work. Its additional work as a speedo cable retainer and breather bolt require little more torque than finger tight. Thus, the solution is to move the battery cable to another attachment location that can more easily satisfy the torque requirement, and then relax the expectations for the remaining Breather Bolt jobs.
To do this with the existing battery cable length means connecting the cable to one of the many gearbox cover bolts. Doing that requires a special "top hat" washer capable of fitting into the counterbored gearbox cover bolt well. I am not aware of a source for this special part, but it turns out to be a simple 15min metal lathe job for the hobbyist. And then secondly, locating a new 6mm gearbox cover bolt that is the length of the original cover bolt, plus the height of the top hat. The special top hat washer then needs to look something like this...
 Section view shown.
Â
[ As an aside: This part represents the best excuse to go ahead and by the metal lathe you've always wanted. Take it from me, the 'significant other' will immediately grasp the need for such a purchase and approve its purchase from the family budget. 🤣Â ]
Assembly of this primary electrical connection will, of course, include coating all parts with an anti-oxidation compound, such as No-Ox-Id. When finalized, the installed part will look like this...
As seen from the Left side.
 As seen from the Right side.
Â
â–ş In your particular case, you'll also want to include a new battery ground cable. One of the primary goals of making any electrical connection, and one that becomes a requirement for high-current terminations, is to be air-tight. In a bolted configuration this can only happen when the fastener head makes a full 360° contact with the lug. When one slots the ring lug to become a "fork", this seal is not only violated, but one runs the risk of the cable terminal spreading and squirting out from under the highly torqued fastener at any time. While I fully understand why this was done, it is a very BAD plan for future reliability. And I do not use that term "reliability" too lightly because that cable not only holds the link to the operation of the electric starter, but also the battery's ability to properly "charge". So a poor connection here is a "double whammy". Take it from me, "you have not lived" until you find yourself in a situation where you need to bump-start a cold Airhead with a dead battery !Â
Hope this helps.
Owning an old Airhead is easy.
Keeping an old Airhead running great is the true test.
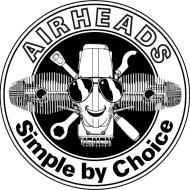
Very helpful! Thanks for the reply and wisdom, Richard.
Depending on the availability of a longer battery cable, perhaps making the connection to the thru bolt located just above the clutch cable seat could forego the custom machining?
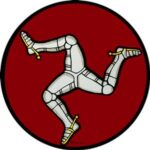
I have tried that, and the problem is not what you'd think ! To do what you describe, you'd need a generic automotive battery cable... which are available at your LAPS in many lengths, starting at about 12 inches.
All commonly available automotive battery cables come with both ring lugs drilled for 5/16" (8mm). So the new cable fits the bolt in question perfectly ! The problem is at the battery end, which needs a 1/4" (6mm) hole.Â
Owning an old Airhead is easy.
Keeping an old Airhead running great is the true test.
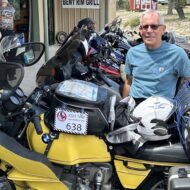
This is where I reinstalled mine, long, long ago. It has worked without issue. Must have bought a generic cable.Â
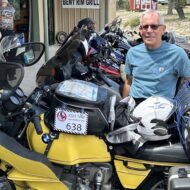
I don’t know how to imbed photos in my reply, so bear with me. The air box then needs a notch like this.Â
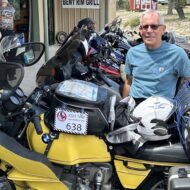
Then, to help my old “nearly stripped” bolt, I tapped for a small set screw to lock it in place.Â
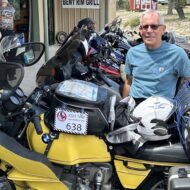
All together, it looks like this. Ground cable is fairly neatly tucked away.Â
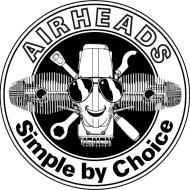
Thanks for the additional posts and solutions.
There’s a couple of companies in the U.S. that one can order custom battery cables from which aren’t very expensive. Any length, any gauge, standard or high-temp marine grade, with a choice of crimped end types and sizes. Lug ends start at 3/16” and go up, with an option to have one or both ends bent 90 degrees.
A bit longer through bolt where I pictured with two stacked nuts might just allow a solid, reliable, and accessible  ground disconnect with no change of stripping a case hole.
I like the set screw solution to lock the speedo cable/case vent bolt. Easier than attempting to re-thread.
Â
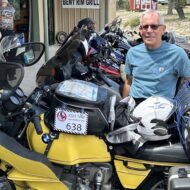
Good solution. Yes, obviously mine is not readily accessible. When I disconnect the ground for other work, I have to do it at the battery.  BMW’s use of that speedo cable / vent bolt is certainly a bit weak. Probably a left-over from previous generations. Here’s to a better ground!
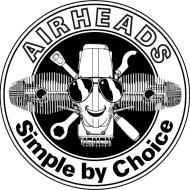
This is why ...... you need to relocate the main ground wire away from THAT hollow Bolt.
On my bikes, I have a ground field, Not just a single main wire to the hollow bolt & frame . . . .
YET when I need to disconnect the ground wire and protect the electronics from a possible spark flash short - - -Â
I still only need to remove 1 wire at the battery negative post.
Â
Â
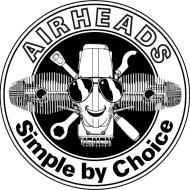
Many ways to skin a cat and all the above suggestions are great for all airheads. But Yippy Ki-A…you’ve got a 1978 R80/7! On your model you should find under the seat, under the right side frame, above the battery, is an unused welded on tab with a hole. That tab has been patiently waiting 34 years for that negative cable end to be attached. Just scrape off the tabs paint for a good ground, and simply bolt the cable end to the tab.Â
Probably not needed but when I reassemble the breather bolt, I replace the removed battery cable lug with the same thickness washer to maintain the original breather bolts position. Not certain, but I assume you could vary the new washer’s thickness slightly, to help catch a few remaining good threads inside the case, just make sure that breather hole remains operational.Â
Ok now the airhead fire-pit "fine point arguments" can commence as to “if the frame is a suitable ground point or not”. But it works fine for this year/model…and it follows the KISS principle!
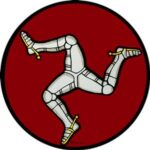
Posted by: @1559This is why you need to relocate the main ground wire away from THAT hollow Bolt.
On my bikes, I have a ground field, Not just a single main wire to the hollow bolt & frame . . . .
YET when I need to disconnect the ground wire and protect the electronics from a possible spark flash short - - -Â
I still only need to remove 1 wire at the battery negative post.
Jim -
You and I are using the same concept, just a different bolt location.
Â
Owning an old Airhead is easy.
Keeping an old Airhead running great is the true test.
- 27 Forums
- 1,900 Topics
- 10.8 K Posts
- 1 Online
- 5,936 Members