Not charging?

At first my thought was my battery was toast as it's been in the bike for a long time but after I thought about it a bit more I'm starting to think the bike is not charging. Does anyone have a suggestion of where to start looking on my '82 R65 LS? I have a Haynes manual that I will look at as well but if someone can give me a faster place to look I'd appreciate it.
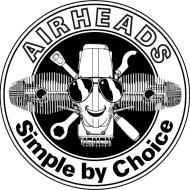
Assuming your bike is OEM equipped, my experience is that a rotor gone open is the most common fault. Next most common would be a bad diode in the diode board. I have only experienced one voltage regulator failure, but in my case the regulator failed to regulate. That caused overcharging and a burnt headlight element and was cooking the battery. Also, brushes on the alternator stator wear down and can loose good contact with the slip rings of the rotor. Of course, crusty or poor wiring connections can give you trouble, even a slightly loose battery cable can cause symptoms. I have never had a stator field winding fail. As far as I know, that is all there is to the airhead charging system. Your Haynes manual might be helpful if it describes test procedures. Do you have a volt/ohm meter? You're going to need one. The first step in testing airhead electrics is a known good battery at full charge. There is a book called "Classic Boxer Electrics" by Rick Jones. That would explain the system and maybe give test procedures. I do not own a copy myself.
former Airmarshal, IL.
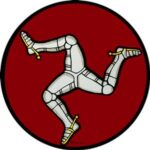
The information James gave you is all excellent information, but I like to check the very simple things first:
• The Airhead charging system cannot work if the incandescent "dashboard" indicator lamp is burned out. You should see the "Gen" lamp glow when the ignition key is turned ON.
• What is the condition of the alternator brushes? Power cannot get to the rotor to "excite" the alternator if either of the 2 carbon brushes are 1. stuck in their holder or, 2. worn short (which reduces the spring pressure) due to mileage.
• What is the condition of the battery terminals ? If the Positive terminal is engulfed in corrosion, then there is a good chance the entire Positive battery cable needs replacing. It is common for battery acid to "wick" under the cable jacket all the way up to the starter motor, which destroys the terminals at both ends of the Positive cable !
Hope this helps.
Owning an old Airhead is easy.
Keeping an old Airhead running great is the true test.

All of the terminals are good, I checked that when I was trying to fit a new battery. I'm not sure the "gen" light is coming in, there are a couple of others that are not. How do you do a fix for that? That unit looks sealed to me.
I haven't looked at the alternator at all yet but I wouldn't be surprised if the brushes are compromised.
Thanks folks, this gives me a couple of things to look at.
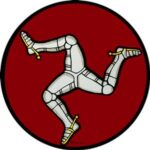
Posted by: @16813All of the terminals are good, I checked that when I was trying to fit a new battery. I'm not sure the "gen" light is coming in, there are a couple of others that are not. How do you do a fix for that? That unit looks sealed to me.
NOTE: It is very nicely sealed, to prevent rain and wash water from killing your 2 gauges.
Unscrew the speed drive cable from the bottom of the speedo. Pop the 3 black plastic dome caps off the screws that point at the riders belly. Under those caps, loosen three #3 Phillips screws about 3 turns only. Slide the gauge unit up and off the steel mounting bracket. When the unit is free of the bracket you will just barely have enough cable slack to roll the gauge unit over and remove the single screw that holds the electrical connector in place. Use a #1 Phillips to remove that screw. While you protect the gauge lens from being scratched... wiggle the large, rubber encased connector out. Once the connector is out, take the gauge unit into your home where you can work on it is an ultra clean and very well-lit area.
NOTE: Inside the gauge unit is the most delicate area of the entire motorcycle. If you cannot work with the soft touch of a brain surgeon and don't posses the fine tools of a clock repairman, then you are better off to stop here and send the unit off to someone who has those skills. You have been warned.
With the gauge unit face down on a soft towel, remove the multiple straight slot screws on the back. The 2 rear covers will lift off to reveal a VERY DELICATE flexible circuit board. Mounted onto the VERY DELICATE circuit board will be 7 or 8 black caps which hold the incandescent bulbs. These caps snap into place, so with very light but steady pressure, rock the black bulb holder back to release each one.
Upon removal you will see how the flexible circuit folds over the bulb holder opening at 2 places at each bulb to allow for the electrical connection. These folded areas of the circuit board are so delicate that they often break. The result of a broken/missing tab is that no power can get to the bulb. So for 8 bulbs you'll have 16 tabs that must be in perfect shape. If even one of them is broken, there is no repair. You must buy a KatDash unit as a replacement. See: https://katdash.com/
If your flexible circuit is still good and retains ALL of its connection tabs, then you can replace the bulbs (except for the GEN lamp) with LED bulb replacements from here: https://www.superbrightleds.com/vehicle-lights/car-boat-light-bulbs
Behind the Red lens you'll want a RED LED; behind the Blue lens you'll want a BLUE LED... and so on. I like for the 2 gauge illumination lamps to be GREEN... especially if you have the /7 green faced instruments. That works out really well.
Re-assembly is the reverse.
IMPORTANT RE-ASSEMBLY NOTES:
► To keep from tearing the delicate "contact tabs" off during reassembly, I highly advise that both the bulb holder's electrical contacts be lubricated using No-Ox-Id electrical anti-oxidation compound.
► Once reassembled, I also highly advise that the double row of electrical contacts on the underside of the gauge unit (Which are exposed to the weather) also be treated with No-Ox-Id electrical anti-oxidation compound.
► The single screw that holds the underside connector should have its threads treated with silicone grease for lubrication. Then the screw should be inserted and turned in a CCW direction until a click is felt. At that point the screw can be turned CW knowing the threads are being re-seated into their original place. The screw should be run down until it touches and then STOP ! If you do not do this then you run a great chance of wallowing out the threads OR pulling out the screw threads, either of which will make your speedo housing unusable.
Hope this helps.
Owning an old Airhead is easy.
Keeping an old Airhead running great is the true test.
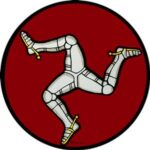
Posted by: @16813I haven't looked at the alternator at all yet but I wouldn't be surprised if the brushes are compromised.
A set of Airhead brushes can be purchased very easily for a minimal ~$5 fee. Of all the Airhead repairs you can do, this one is one of the very, very lowest cost. So it's crazy to go through the work of opening the front cover "just to look". A better plan is to have 2 new brushes ready and simply replace whatever you find. This is especially true if you have no idea of the brushes' age or mileage.
Then you can ride your Airhead for the next 10 years knowing whatever is going wrong, it's not the alternator brushes !! 🤣
Hope this helps.
Owning an old Airhead is easy.
Keeping an old Airhead running great is the true test.

Ok, thanks for that little guide to the gauges. I'm hoping I don't have to dig into that. Any thoughts on the best place to buy brushes?

Thanks for the offer but I ended up ordering some from Bob's. I needed a couple of the rubber plugs the go in the engine case where you look for TDC. As you said they were cheap.

The brushed arrived, I'll get them installed and see where I'm at.
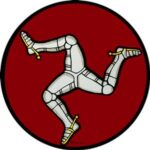
You'll remember that new brushes was only one of several suggestions.
Owning an old Airhead is easy.
Keeping an old Airhead running great is the true test.

When I opened it up one of the brushes was pretty much gone so I'm confidant that was the problem. Now I need to get the soldering iron out to remove that cover from the stator and solder in the new brushes. wish me luck I'm not very good at soldering.

Of course whatever solder they used is crazy hard, none of my soldering irons will melt it. I'm going to bring in my grinder to take them down.
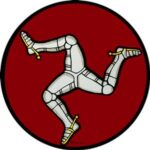
✦ You're correct, the factory brushes are soldered to the brass brush holder. The secret of soldering is the application of HEAT. That means remove the old brushes and get rid of any other metal parts attached to the brass holder. This because those extra parts will keep the temperature from getting high enough to melt the solder. I remember doing my brushes with a Weller soldering gun that wasn't particularly a high wattage device. So it can be done if you clear the excess mass.
✦ It's been years since I did that job, but I also remember seeing a small tab built into the brass brush holder. This means you can crimp a terminal onto the new brush leads while they are still on the bench. Then fitting the brushes involves no soldering. I don't know that the tab is present on all models, but you can look.
✦ The lesson here is that big issues typically start with the simplest causes. Checking simple maintenance items once a year or while you have the cover off to look at other parts can save you a LOT of future trouble. When you ride a Classic or Vintage bike, the key is all in PREVENTATIVE maintenance.
Hope this helps.
Owning an old Airhead is easy.
Keeping an old Airhead running great is the true test.
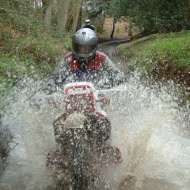
HI I drilled my solder points on brushes out, then soldered new ones in, then check alternator light, check stator , final project the wire between the b+ point on diode board and started motor is super thin for the power it carries, I made a new one up twice the size never had charging problem again always have 14.2 volts

Good to know.
- 27 Forums
- 1,900 Topics
- 10.8 K Posts
- 3 Online
- 5,936 Members